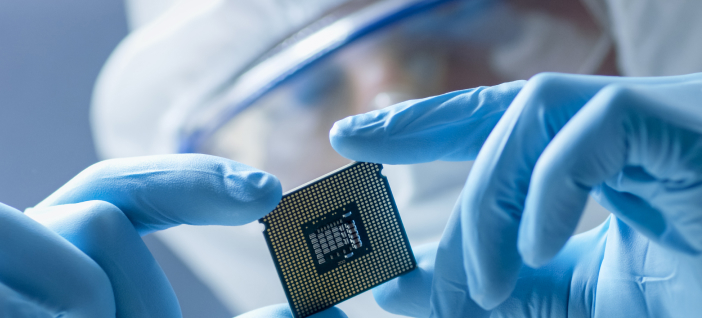
The CHIPS Act has sparked a resurgence of investment and optimism in the semiconductor industry, promising to create more than 33,000 new manufacturing jobs in the U.S. However, this $52 billion initiative comes with one major obstacle: a shortage of skilled frontline workers.
We are projected to face a deficit of 67,100 technicians, computer scientists and engineers throughout the semiconductor industry by 2030, according to a report released by the Semiconductor Industry Association and Oxford Economics. Some reports estimate this shortage to be as large as 2.1 million semiconductor jobs by 2030.
The CHIPS Act has reserved $9 billion in workforce development funding, specifically to address the anticipated skilled labor shortage. However, funding alone won’t close this gap. It’s going to require semiconductor manufacturers to spend this money wisely by addressing three critical challenges:
Challenge #1: Recruiting and hiring skilled workers
The new, highly automated smart semiconductor manufacturing facilities won’t resemble today’s production lines. A typical fab will house at least 2,000 distinct tools, each comprising over 5,000 components. While these tools are smart, like any tool they break, even a slight production glitch or equipment malfunction, requires highly skilled technicians to quickly diagnose and resolve the issue to prevent costly downtime.
With skilled semiconductor technicians in short supply, attracting top talent requires semiconductor companies to differentiate by reimagining how they train and upskill frontline workers. They must first acknowledge that highly skilled technicians want opportunities to gain advanced expertise and take on expanded roles over time. This necessitates a long-term commitment to designing and implementing personalized learning plans that systematically equip technicians with the skills required for advancement within their organization. By communicating their commitment to invest in technicians’ professional development during the recruiting process, coupled with showcasing “internal social proof” of how they accomplish this, semiconductor companies can better differentiate and compete for skilled workers.
Attracting skilled technicians is just the first step. To retain them, manufacturing executives must invest in advanced learning & development technologies, such as a learning management system (LMS). An LMS is an essential tool for systematizing training processes, digitizing content, and standardizing training delivery and certification, all while supporting personalized learning. A comprehensive, operationally integrated LMS that ensures competency and equips technicians to advance through the ranks will keep your frontline workers engaged and productive, which is crucial for maintaining a motivated, capable, and loyal workforce.
Challenge #2: Consistently reducing time-to-productivity for new hires
In the semiconductor industry, every minute counts when it comes to ramping up production and shortening delivery times. Informal onboarding and unstructured training processes significantly delay the time it takes for new hires to become fully productive team members. This impacts production schedules and increases costs associated with underutilized labor.
The challenge – addressing inconsistent, manual onboarding, training, and certification practices through systemization. Semiconductor manufacturers must streamline their onboarding and training programs through consolidation and systemization to focus on consistently developing critical skills and knowledge required for each role. This involves structuring training requirements around formalized induction, including a combination of general onboarding and compliance programs, with factory and module/work area-specific role-based training requirements. Systemized On-The-Job skills-based training (OJT) supports this, which provides module, tool, and task-based training plans, skills assessments, and signoff practices using a structured pathway approach.
This holistic, systemic approach reduces variance in training effectiveness, better aligning to the motivations and needs of both the worker and workplace, creating happier, more productive workers. This is proven to reduce time to productivity by an average of 40% while increasing retention rates – especially in the crucial first 90 days of hire.
Implementing an advanced LMS that enables personalized, just-in-time learning experiences combined with effective, consistently applied role and task-based training is critical for engaging and retaining these workers during this crucial period.
Challenge #3: Measuring onboarding and training effectiveness
Investing in onboarding and structured but flexible skills-based training programs is a necessary but significant undertaking for fabs, and these programs must deliver the desired results in terms of worker performance, productivity, and safety.
Before you start though, it’s important to plan to measure the effectiveness of your onboarding and training programs as you can’t improve what you don’t measure. Without specific goals you plan to achieve, you will have no idea whether you are on the right track to success or not. At the same time, if you can’t prove value through measurement of actual achievement vs goals (which in turn are tied to key business performance KPI’s), your ability to secure further executive support and funding will be challenging.
To effectively measure and improve the effectiveness of these programs, establish clear people performance metrics that are impacted by training and align with production KPI’s – examples include:
- Total output %
- % yield
- Scrap rate
- Customer return rate
- Cycle time
- On-Time-Delivery
- Days without a safety incident
- Equipment availability
- etc…
Training program reach, bench-depth, quality, completion rates, and behavioral change indicator metrics, amongst others, can all be used to ensure aligned people effectiveness goals are set and can be measured and correlated with tangible business success outcomes. For general training and skills areas, you can collect data on training completion rates, time-to-productivity, employee retention, and job performance, among other metrics. Regularly analyzing this data enables you to identify areas for improvement, demonstrate how training and certification positively impact key business performance indicators, and help you make informed decisions about training content, delivery methods, and support resources for realizing even greater value.
This requires a comprehensive LMS solution that can effectively capture and analyze data on learner engagement, performance, outcomes, and certification status across all your sites, with absolute data and trend analytics capabilities. To maximize your ability to truly leverage this data to prove value, opt for an LMS that enables training managers to quickly:
- Identify and address skills gaps
- Update training content based on feedback and performance data
- Monitor certification credentials for upcoming expirations and proactively manage re-certification processes,
- Measure the ROI of training investments over time.
For example, if you can show a reduction in time spent manually reviewing and managing certification status, a task prone to human error, you can translate that into tangible cost savings for your business. It’s important to note that ‘facts tell, stories sell’. So, you also need to provide an easily understandable narrative of your success metric data that proves your impact in terms that your audience will relate to. This example focusing on the cost-saving from effective training is a strategy sure to get your leaders excited about and supportive of further expanding your workforce development programs.
With the semiconductor industry facing a potential deficit of more than two million workers by 2030, every investment in workforce development must deliver maximum impact. Measuring the effectiveness of onboarding and training programs is not just a best practice, it’s a necessity for ensuring the industry can meet its urgent talent needs. Leveraging a modern LMS with robust data analytics capabilities is essential for making data-driven decisions and continuously optimizing these programs.
The time to act is now. With the semiconductor industry poised for unprecedented growth and facing a critical shortage of skilled workers, manufacturers must move quickly to implement strategic workforce development initiatives. By taking advantage of the workforce development opportunities provided by the CHIPS Act and strategically investing in personalized, data-driven training powered by advanced learning management systems, semiconductor manufacturers can cultivate the highly skilled frontline workforce necessary to drive innovation and bolster competitiveness.
The stakes are high and the competition for talent is fierce. So, what are you doing to ensure you have a workforce that can compete effectively in the post-CHIPS Act business world?
If you are concerned about your operational workforce talent strategy – talk to us. Seertech has extensive experience helping semiconductor manufacturers address critical workforce challenges through advanced learning technologies. Contact us to schedule a no-cost consultation to discuss how to design and launch your training initiatives and establish a foundation for your skilled workforce’s long-term success and retention.
For more insights on how manufacturers can overcome the industry’s talent gap, download The Great Skill Shortage.
Recent articles
10 Brutal Truths About Learning Metrics (and What to Track Instead)
Most learning dashboards are full of data. But the question is: does that data actually prove anything? If your reports are still tracking completions, time spent, or learner satisfaction, you’re not alone. But you’re also not showing impact. Business leaders are asking for results, not activity. It’s time for L&D to trade vanity metrics [...]
Overcome Training Scalability Challenges with an Extended Enterprise LMS
Understanding Customer Education as a Strategic Priority In today’s competitive business environment, customer education isn’t just a support function — it’s a strategic lever for driving engagement, retention, and long-term success. When customers understand how to fully use your product or service, they see more value. That leads to better adoption, deeper satisfaction, and [...]