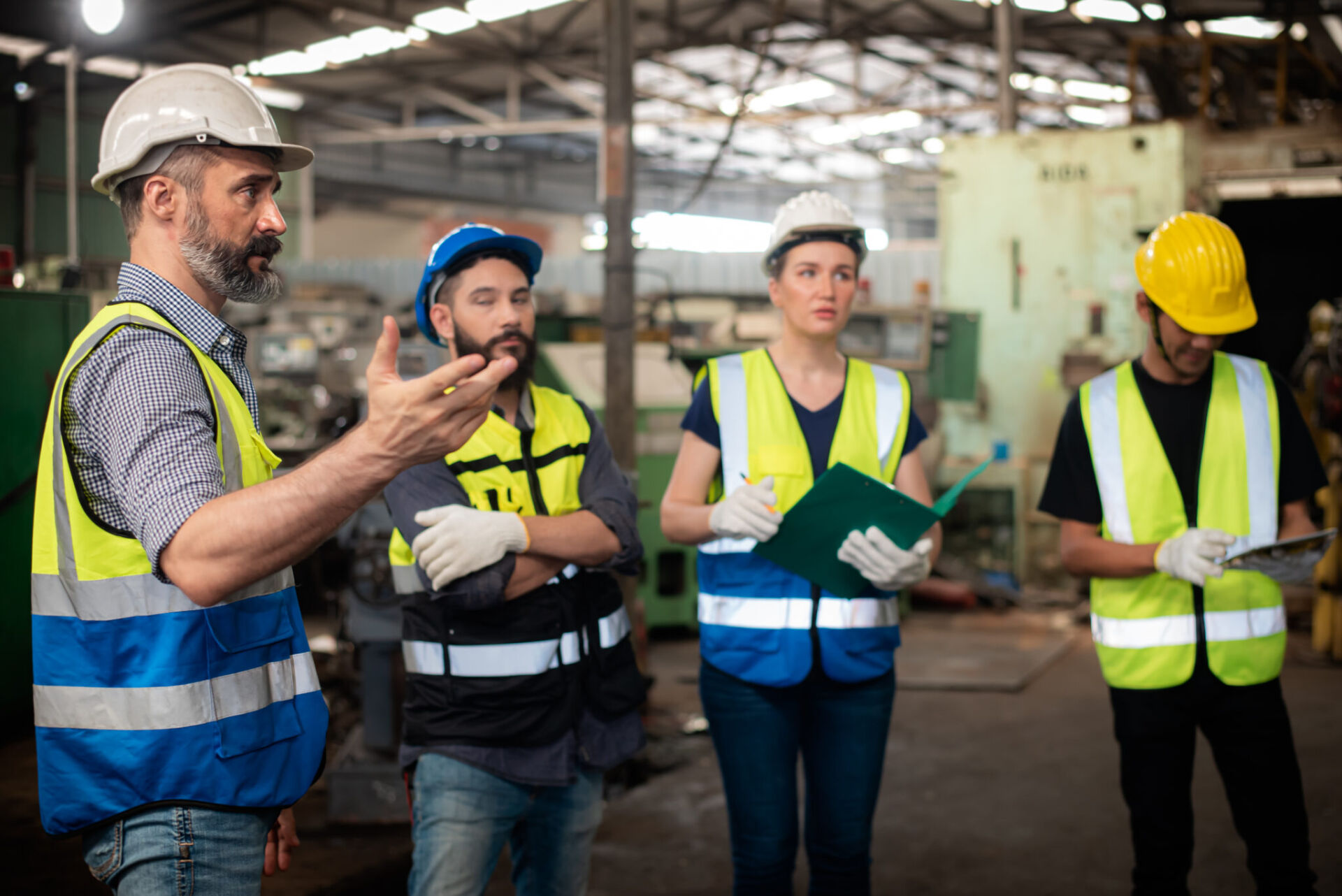
In today’s fast-paced business world, manufacturers constantly seek ways to improve productivity and quality. However, one critical yet overlooked challenge in achieving this is the proliferation of tribal knowledge within organizations.
While tribal knowledge may seem like a convenient way to train a new employee, it poses a significant threat to production quality. In this article, we’ll explore the concept of tribal knowledge, its potential impact on production quality, and effective strategies for mitigating the risks it poses.
The Origins of Tribal Knowledge
The term “tribal knowledge” originated from the concept of indigenous tribes and their unique customs, beliefs, and practices that were passed down through generations. In today’s business context, tribal knowledge refers to the collective knowledge and experience of a group of individuals within an organization.
Tribal Knowledge includes the unwritten, unspoken, and undocumented knowledge and practices shared among a group of employees. This knowledge is often passed down through trial and error and informal interactions rather than formal training or documentation. In manufacturing environments, equipment repair technicians often suffer the most severely from tribal knowledge, including unofficial shortcuts and repair tips.
The Risks of Tribal Knowledge
Relying on employees’ tribal knowledge can be a way to rapidly launch a small organization. It provides a degree of freedom and adaptability, enabling employees to quickly change their processes on the fly without a formal change review process. However, in large manufacturing organizations focused on minimizing variabilities and improving quality control, the very nature of tribal knowledge poses a serious risk. Let’s review the risks.
Limited Access and Knowledge Gaps
One of the biggest risks of tribal knowledge is that it is often not documented or recorded, making it difficult for new employees to access. This creates knowledge gaps and limits the ability of new employees to fully understand their roles and responsibilities, resulting in slow and poor onboarding experience.
Additionally, if only a few individuals possess critical knowledge, it can create a bottleneck in decision-making and problem-solving processes. In many factories, there is an over-reliance on the few experienced “experts” on various tools which further increases the knowledge gap in the organization. Consequently, this will cause interruptions to the production, tool uptime, and compromises overall quality of the work.
Inconsistent Processes and Procedures
Tribal knowledge leads to inconsistencies in organizational processes and procedures. When knowledge is passed down through word of mouth, there is a higher risk of misinterpretation or miscommunication. This results in different employees following different processes for the same task, leading to confusion and errors. This adds negative variables to the manufacturing process and degrades the overall process capability index, CpK.
Wrong Processes and Procedures
Tribal knowledge culture frequently enables the development of unofficial shortcuts based on an individual’s informal trial-and-error experiments. Without carefully designed testing and data analysis, these shortcuts may not be an effective method, potentially compromising the long-term integrity of factory equipment.
Resistance to Change
Another risk of tribal knowledge is that it can create organizational resistance to change. Employees who have grown accustomed to developing their own practices or techniques may firmly believe that these methods are optimal, as they perceive their circumstances to be distinct and unparalleled. Have you ever heard, “Our factory is different from others, and that solution won’t work here.” This type of siloed culture thinking is commonplace in large organizations with multiple factory locations.
This resistance hinders innovation and prevents manufacturers from adapting to changing market conditions or industry shifts. It can also lead to a lack of flexibility and agility, which are essential for staying competitive in today’s business landscape.
Managing Tribal Knowledge
While it may seem like tribal knowledge is an inevitable part of any organization, there are ways to manage it effectively to minimize its impact on production quality. Here are some strategies for managing tribal knowledge.
Document Critical Knowledge
The first step in managing tribal knowledge is identifying undocumented practices carried out by employees. This might require shadowing frontline technicians in the factory and closely observing the flow of work.
By improving documentation, all employees will have access to the golden standard, the single source of the truth. This prevents knowledge gaps and ensures uniformity in processes and procedures that employees follow.
Foster Learning Culture and Open Communication
Another way to manage tribal knowledge is to cultivate a culture of continuous learning and open communication throughout the organization. By creating a culture of knowledge sharing and robust feedback mechanisms between the frontline employees and engineering, best practices can be consistently reviewed and updated in the official documentation.
This culture not only enables faster identification of potential process flaws that are quality risks but also fosters a sense of community and collaboration. By openly discussing the pros and cons of the practices and highlighting areas for improvement, teams can work together to enhance efficiency while upholding quality. Encouraging inputs from all team members ensures an open and constructive dialogue aimed at continuous improvement.
Embrace Technology
Technology plays a significant role in mitigating tribal knowledge. By implementing a comprehensive learning management system (LMS), organizations can establish a centralized repository for all critical knowledge and systematically manage the delivery of training activities. This can include documents, videos, and other resources that employees can access at any time.
A capable LMS can also provide content revision controls and automate notifications when a new version has been published. By providing employees with quick access to the most up-to-date information, it ensures they are following the latest procedures.
Structure On-The-Job Training
Without a systemized training solution designed for frontline workers, organizations will continue to proliferate tribal knowledge and practices. A more structured and technology-driven approach to on-the-job training (OJT) is a requirement for all mission-critical businesses.
Seertech has pioneered an automated and structured technology solution called OJT3, designed to streamline and control the knowledge and skills transfer process. Leveraging the ‘Power of Three’- Plan, Execute, and Prove, OJT3 digitizes the entire OJT workflow, encompassing resource planning, bench capability analysis, and skills evidence capture. This guarantees that shop floor training is executed with the consistency and structure of traditional classroom training, all while offering practical learning in the flow of work.
Seertech has a track record for helping organizations improve quality, employee training, and costs. Contact us for a free consultation and explore how you can leverage our experience to elevate your business
Recent articles
10 Brutal Truths About Learning Metrics (and What to Track Instead)
Most learning dashboards are full of data. But the question is: does that data actually prove anything? If your reports are still tracking completions, time spent, or learner satisfaction, you’re not alone. But you’re also not showing impact. Business leaders are asking for results, not activity. It’s time for L&D to trade vanity metrics [...]
Overcome Training Scalability Challenges with an Extended Enterprise LMS
Understanding Customer Education as a Strategic Priority In today’s competitive business environment, customer education isn’t just a support function — it’s a strategic lever for driving engagement, retention, and long-term success. When customers understand how to fully use your product or service, they see more value. That leads to better adoption, deeper satisfaction, and [...]