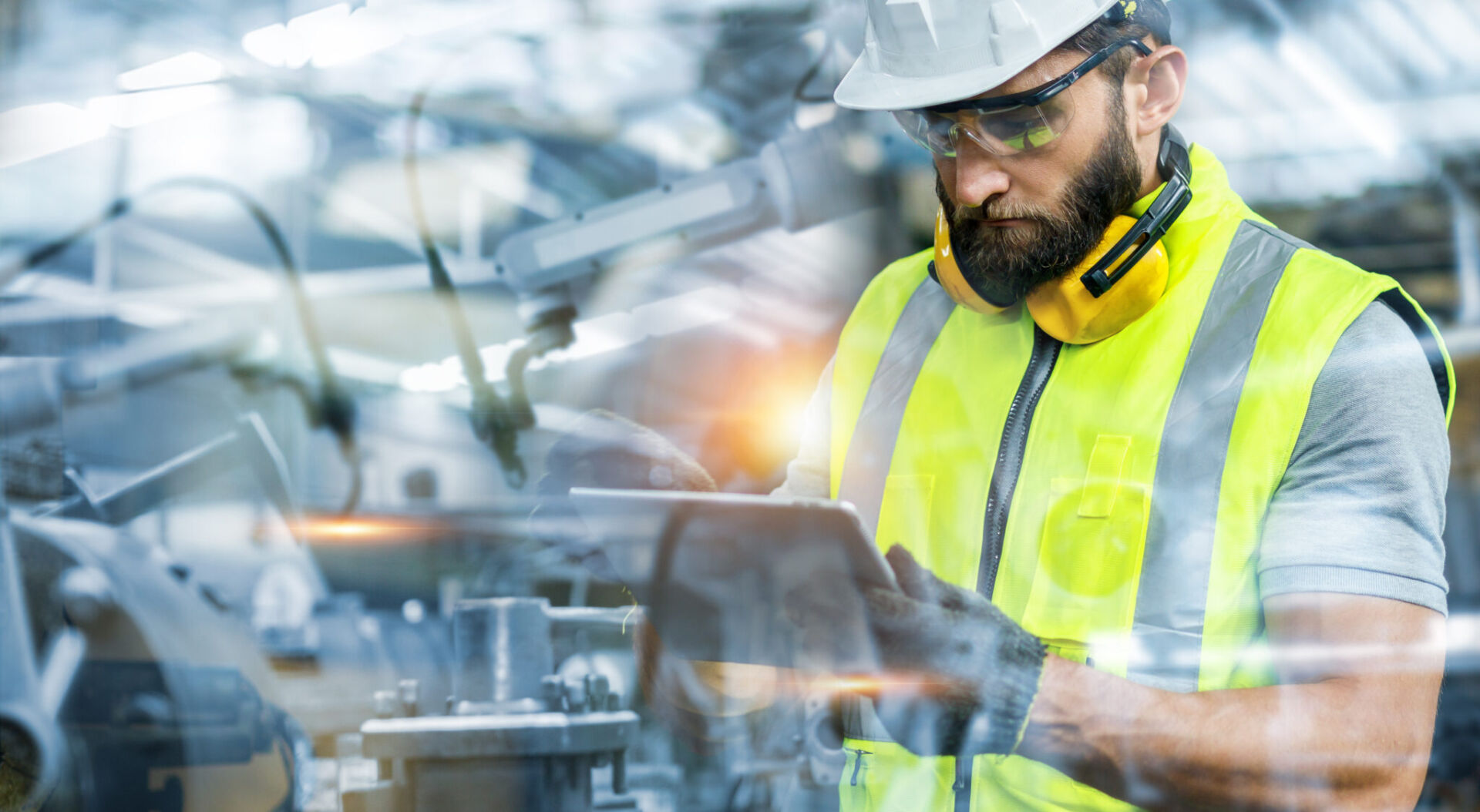
Despite the advancements in smart manufacturing technologies, the reliance on traditional on-the-job training (OJT) methods is seriously impacting the transition to the smart factory. It’s actually costing you money, and the longer you leave this unaddressed, the worse it’s going to get.
Here’s why:
More Complex Skills Required:
With advancements in smart manufacturing, the sheer volume and complexity of robotics, sensors, and data analytics have increased sharply. This has reduced the need for factory operators who perform more basic and manual tasks while sharply increasing the demand for technicians who are capable of maintaining sophisticated factory equipment.
Lack of Structured Learning:
Typically, factory employees learn most of their job skills inside the factory while on the job, alongside their peer trainers, not asynchronously in a classroom setting or via e-learning. Traditional OJT is often informal, lacking structure and consistency. This results in ad-hoc training experiences that fail to adequately prepare workers for the complexities of smart manufacturing environments. Without a standardized curriculum and training framework, the learning outcomes and production quality are more variable and unpredictable. Investing in a structured approach to learning and development is not only a smart business decision, but it’s also crucial for maintaining a competitive edge in today’s fast-paced world.
Inefficiency and Inconsistency:
Manual OJT processes are all too often time-consuming and inefficient, requiring significant resources to coordinate and manage. At the same time, the quality of training can vary depending on the trainer’s expertise and availability, leading to inconsistencies in skill development among workers. More disturbingly, employees often share incorrect tribal knowledge with others, compounding the impact on production quality.
Higher Employee Turnover:
Unstructured OJT lacks peer trainer accountability because their assignment as a trainer is often undocumented and subject to competing job priorities that are more important than training. Quality training outcomes are impacted by variable ability of the trainer, so a systemized solution assigning qualified and available trainers to OJT is crucial. Without a systemized solution, new hires encounter a poor onboarding experience, which leads to higher turnover, further exacerbating the skills gap problem.
Limited Scalability:
Traditional OJT methods are not easily scalable to accommodate the growing workforce needs of smart manufacturing. As industries expand and adopt new technologies, the demand for skilled workers increases exponentially, making it challenging to provide comprehensive training to all employees in a timely, consistent, and cost-effective manner.
Missed Opportunities for Innovation:
Informal and undocumented peer-to-peer OJT often focus primarily on job-specific tasks and responsibilities, neglecting higher-level concepts and emerging technologies relevant to smart manufacturing. This narrow focus limits workers’ exposure to innovative ideas and best practices, stifling creativity and inhibiting organizational growth.
Risk of Knowledge Loss:
The manufacturing industry is facing an aging workforce, and there is a significant risk of widespread knowledge loss as experienced workers retire or leave the company. Without formalized training programs and knowledge transfer mechanisms in place, valuable expertise and institutional knowledge will be lost, posing challenges for succession planning and production continuity.
To overcome these challenges and unlock smart manufacturing’s full potential, organizations must transition from traditional OJT methods to more structured and technology-driven training solutions. By investing in advanced training technologies and methodologies, organizations will unlock their investment in smart manufacturing by ensuring that their workforce is equipped with the skills and knowledge needed to competitively thrive in this new era of smart manufacturing.
A Question for You:
Is your organization currently operating with unstructured OJT practices? Can you relate to these pain points?
If the answer to the above question is yes, finding the right solution partner is an important first step to exploring options and best practices. Seertech has developed an automated and structured technology solution called OJT3, designed to modernize the OJT experience. OJT3 uses the ‘Power of Three’: Plan, Execute, and Prove to fully digitize the OJT workflow from planning to bench capability analysis and evidence capture. OJT3 delivers the consistency and structure of traditional classroom training while offering practical learning in the flow of work on the actual factory floor. Contact us for a free consultation and explore how you can leverage our experience to drive your smart manufacturing initiatives.
Recent articles
Overcome Training Scalability Challenges with an Extended Enterprise LMS
Understanding Customer Education as a Strategic Priority In today’s competitive business environment, customer education isn’t just a support function — it’s a strategic lever for driving engagement, retention, and long-term success. When customers understand how to fully use your product or service, they see more value. That leads to better adoption, deeper satisfaction, and [...]
The Ultimate Guide to Tracking LMS Metrics
Understanding the Importance of LMS Metrics Understanding LMS metrics is crucial for the success and validation of your learning programs. LMS metrics offer key insights into the effectiveness of training initiatives, helping to provide concrete evidence of their value. With increasing pressure to demonstrate ROI, particularly from senior leadership and financial officers, tracking these [...]