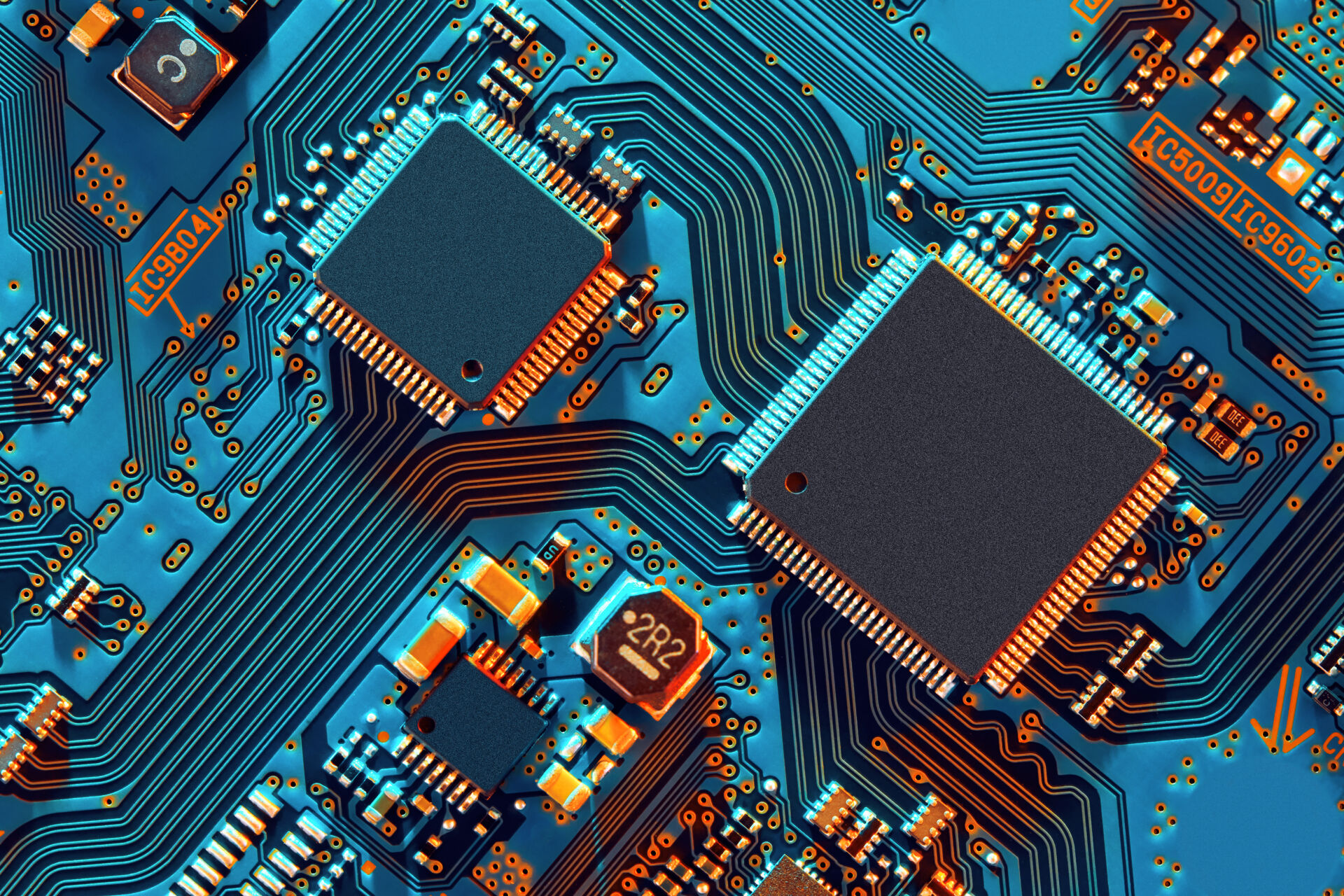
At this year's SEMI FOA Collaborative Forum, one message stood out loud and clear: the semiconductor market is on track for a recovery in 2025. Surging investment in AI data centers, the passing of the global chips legislation (CHIPS Act and European Chips Act), and global fab expansions are all set to fuel the growth for the next few years.
But as industry leaders discussed these forecasts, a critical challenge still remains—whether the workforce will be ready to meet this moment.
As an invite-only event, FOA brought together some of the biggest names and sharpest minds in semiconductor manufacturing. Here are some of the top market trends our team gathered and what they mean for the workforce as we look ahead.
The $1 Trillion Market Is Coming—Fueled by AI and Chip Demand
According to experts at FOA, the semiconductor industry is projected to reach $1 trillion by 2030, growing at a 10% CAGR from 2023. Much of this growth will be driven by AI, data centers, and high-performance computing (HPC)—and it's happening fast.
Here are a few of the key takeaways from SEMI's latest research:
- IC (integrated circuit) sales are expected to grow 23% YoY in Q1 2025 alone, driven by AI demand.
- AI-related investments in chips are projected to surpass $250 billion in 2025. (Source: Company data, Morgan Stanley, SEMI estimate)
- Fab capacity is scaling up significantly, with 300mm fabs adding 5.1 million wafers per month (wpm) by 2026—a 29% capacity increase.
- Total semiconductor equipment investments are forecasted to hit $113 billion in 2024, with steady growth into 2025 and beyond.
Taken together, this signals an acceleration in production, capacity investments, and technological advancement—but also a strong demand for skilled, agile, and prepared workers.
The Workforce Gap: Two Challenges That Could Hold the Industry Back
1. Upskilling Your Existing Workforce—Fast
One of the key issues raised at FOA was the challenge of developing a strong workforce to keep pace with rapid technological change. AI and machine learning are reshaping semiconductor manufacturing, pushing companies toward smart automation and next-generation production processes.
But without a workforce that can operate, adapt, and innovate within these new systems, investments in automation and AI will fall short. The message from leaders was clear: if your teams aren't ready to work in AI-enabled environments, you're going to struggle to keep up—let alone lead.
Unfortunately, many companies are finding that current training models are too manual, too inconsistent, or too disconnected from real operational needs. In a market moving this fast, agile, effective upskilling isn't just a nice-to-have—it's a competitive necessity.
2. Capturing and Retaining Knowledge Capital Before It Walks Out the Door
A second, equally pressing challenge is retaining knowledge capital as the industry grapples with retirements and turnover. With new fabs coming online and existing ones modernizing, the loss of experienced technicians and engineers means losing years—sometimes decades—of critical operational knowledge.
The problem is compounded by the fact that much of this knowledge is "tribal"—undocumented, passed down informally, and essential for maintaining quality and efficiency on the shop floor. If that knowledge leaves with retiring workers, companies face steep learning curves, costly mistakes, and operational disruptions.
Semiconductor companies recognize that capturing and standardizing this knowledge has become one of the industry's most urgent needs, especially as fabs grow larger and more complex. But doing so requires a systematic, strategic approach—not just ad hoc mentoring or outdated training manuals.
Why Now: The Takeaway for Industry Leaders
The question for decision-makers isn't whether the market is coming back—it's whether your workforce will be ready to support it when it does come back. With $250 billion in AI-driven chip investments, a projected 23% surge in IC sales, and massive fab expansions underway, companies that can't keep their workforce aligned and up to speed will find themselves at a serious disadvantage.
More importantly, as AI and automation change the nature of work on the factory floor, companies need to reimagine how they develop and retain expertise—both for today's challenges and for the next decade of innovation.
Here are three key workforce takeaways:
- Upskilling needs to happen faster and smarter. Traditional training methods won't keep pace with the rate of technological change. Companies need solutions that help employees learn in the flow of work—targeted, scalable, and aligned with operational priorities.
- Knowledge retention is a strategic priority. Companies must move beyond informal knowledge sharing and start systematically capturing and distributing critical know-how, especially from senior experts and specialized technicians.
- The workforce is as important as technology. AI, automation, and advanced equipment are only as effective as the people operating them. Investing in workforce readiness is investing in operational success and competitive advantage.
Final Thought: The Workforce Is the Next Frontier
As the semiconductor industry braces for the next growth cycle, workforce development isn't a secondary concern—it's the next frontier. The companies that will thrive in this next era are the ones that invest in their people to grow—equipping them with the skills, knowledge, and confidence to drive innovation from the ground up.
As we continue conversations from FOA, we're keen to hear how others in the industry are tackling these workforce challenges. How is your team preparing for what's coming next? Let's keep the conversation going—because if the market is rebounding, our people need to be ready to rebound with it.
Recent articles
The Foundations of Learning ROI: How to Align L&D with Business Goals
If you want to prove the return on investment (ROI) of your learning programs, you can’t start with course design. You can’t even start with learning objectives. The first step is far more strategic: align learning to the outcomes the business actually needs. For many organizations, this requires a shift in mindset. Learning can [...]
Why ROI Matters More Than Ever in Learning and Development (L&D)
The Business Climate in 2025: Why L&D Can’t Afford to Fly Under the Radar To understand why ROI matters more than ever, we have to look at the broader business context. In 2025, companies are under immense pressure to preserve margins, drive performance, and stay competitive, often with fewer resources than before. Inflation, shifting [...]