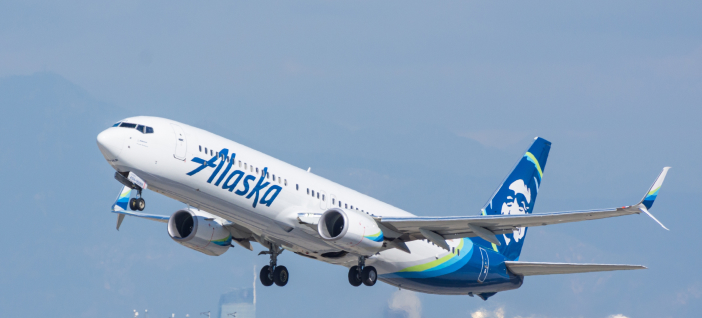
On March 10th, 2024, multiple news outlets reported that the DOJ launched a criminal investigation into the door plug blowout on a Boeing 737 Max 9 plane during an Alaska Airlines flight in January. Boeing acknowledged that they cannot find documentation for the work done on the plug door panel on the 737 Max during the assembly, even though this is a requirement.
Although the final root cause of this event is pending further investigation, this incident serves as a stark reminder of the significant role that rigorous quality control, documentation, and employee competence play in ensuring the safety and reliability of an aircraft. But it’s also important to acknowledge that critical errors like this can happen to any mission-critical organization, regardless of industry.
Fragmentation – The Enemy of Quality
For mission-critical industries like manufacturing, documentation serves as the backbone of accountability, traceability, and regulatory compliance. It includes documents such as design specifications, maintenance procedures, maintenance logs, test results, employee training records, and much more. A key quality challenge for over 80% of organizations is that critical documentation and evidence are managed in different systems. These fragmented systems often don’t talk to each other, increasing quality risk through a lack of effective information flow management and an incomplete chain of evidence.
Quality is Not Optional
Quality control isn’t just a process; it’s a non-negotiable, ongoing commitment to excellence. From equipment selection to manufacturing processes to employee competency management, every aspect of a mission-critical organization must adhere to strict quality control protocols. Effective quality control isn’t merely about checking the boxes; it’s about promoting a quality culture by empowering all employees to identify and address potential gaps before they pose risks to customers. Empowerment needs to be supported by consolidated and integrated quality systems that promote effective quality practices.
A Wake-Up Call
Boeing’s emergency landing serves as a wake-up call, sounding the alarm on the dire consequences of lax documentation and quality control in any organization. It’s a timely reminder of the cost of failing to proactively prioritize a robust Quality Management System which can have catastrophic ramifications, tarnishing reputations and eroding public trust.
You Can’t Afford Poor Quality
We all think it won’t happen to us, but even the largest organizations aren’t immune to the effects of poor-quality management systems. A key to robust quality control is implementing a systemized and centralized strategy to manage documentation, change revision tracking, employee communication, and employee training against those documents. This type of enterprise strategy requires strong leadership to execute change management and cultivate a quality-first employee culture.
A Question for You
Is your organization at risk due to poor quality management practices and fragmented quality systems? Can you afford the risk?
If the answer to the above question is yes, and your organization is ready to heed this wake-up call, finding the right solution partner is an important first step to exploring options and best practices.
We have focused on consolidating mission-critical quality systems for over 20 years. Contact us for a free consultation and explore how you can leverage our experience to mitigate your quality systems risk and avoid consequences detrimental to your business using our OJT3 framework.
Recent articles
Overcome Training Scalability Challenges with an Extended Enterprise LMS
Understanding Customer Education as a Strategic Priority In today’s competitive business environment, customer education isn’t just a support function — it’s a strategic lever for driving engagement, retention, and long-term success. When customers understand how to fully use your product or service, they see more value. That leads to better adoption, deeper satisfaction, and [...]
The Ultimate Guide to Tracking LMS Metrics
Understanding the Importance of LMS Metrics Understanding LMS metrics is crucial for the success and validation of your learning programs. LMS metrics offer key insights into the effectiveness of training initiatives, helping to provide concrete evidence of their value. With increasing pressure to demonstrate ROI, particularly from senior leadership and financial officers, tracking these [...]