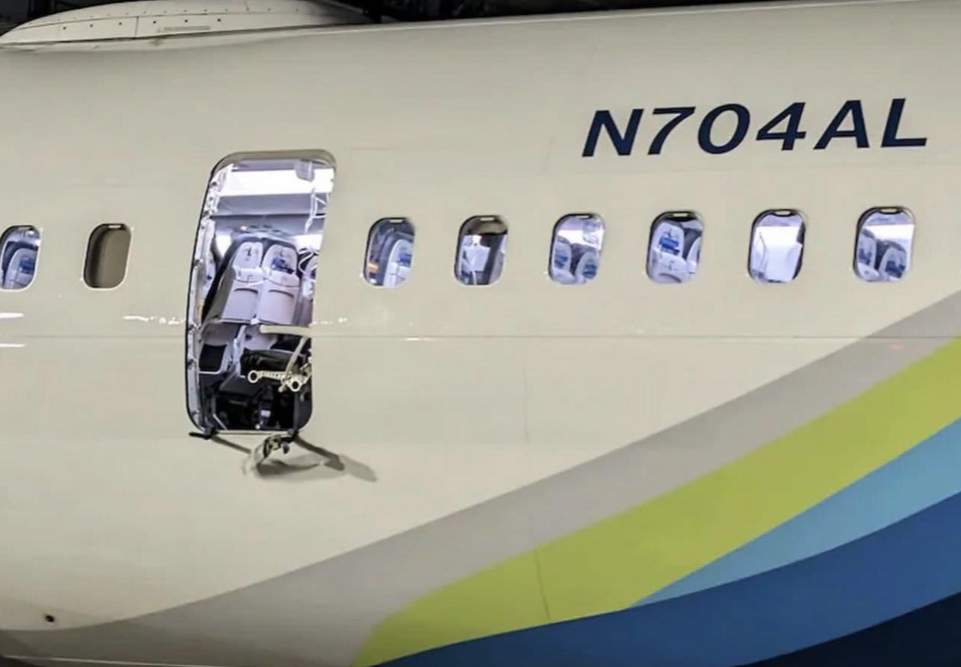
If you have been keeping up with the news recently, you probably recognize this photo. Alaska Airlines Boeing 737-9 Max, departing from Portland, OR on Jan 5th, 2024, had to make an emergency landing when a cabin panel (plug door) blew off in midair, causing an explosive decompression of the cabin. Fortunately, no injuries were reported.
The initial investigations conducted by Alaska Airlines, Boeing and the National Transportation and Safety Board (NTSB) points to loose, or potentially missing bolts that secures the plug-door. They are investigating the possibility of manufacturing flaws.
Many news outlets have quickly blamed Boeing and its subcontractor for prioritizing short-term profit over production safety and quality. Some even report that the subcontractor employees were told to falsify records after the inspection team found excessive defects on parts made for Boeing. Time will tell if some of these accusations are true or false, but the news outlets have jumped on the opportunity to sensationalize the story.
What is clear is that incidents like this will have far-reaching financial consequences for every company involved. On top of that, the company’s brand will suffer and even more importantly, the authorities will carefully investigate their quality control processes. This is a good reminder that quality control system is a business-critical process that requires robust strategy and continuous improvements, so let’s take a deeper look.
Quality Control requires rigor and discipline
Anyone working in a complex manufacturing organization understands the importance of developing a robust quality control to reduce defects and lower cost. Various methodologies have been developed over the last 50+ years to improve the overall quality. Some of the more commonly used tools are:
- Lean 6sigma manufacturing
- TQM (Total Quality Management)
- Value Stream Mapping
- FMEA (Failure Mode and Effects Analysis)
- SPC (Statistical Process Control)
- 5S
- 5 Why Root Cause Analysis
Using these types of techniques, manufacturing organizations are constantly striving to make improvements to their processes and their equipment. They carefully characterize their processes and equipment capabilities by running DOE (Design of Experiments), and then they implement an optimal control mechanism to ensure defect-free production. This ongoing effort is often called the CIP (continuous improvement process).
While many manufacturers spend a significant number of resources on process and equipment optimization initiatives, there is one element that some organizations do not spend enough time to fully characterize and control – the human element.
What is the human factor & “Swiss Cheese” model
The human factor in complex organizations is very difficult to model because humans are inherently unpredictable, and behaviors are random. To explain the randomness in the context of risk management, a psychology professor at Manchester University named James Reason developed a “Swiss Cheese” model. He documented this concept in his book, Human Error, released in 1991. In this book, he explains that failures like aircraft accidents and medical mishaps are not a result of one or more independent events. Instead, failures and errors occur due to several interconnected factors making up the system.
[Learn more about Swiss Cheese Model Here]
The image of “Swiss Cheese” is a metaphorical representation of a complex system where each slice of cheese represents a barrier to catching the error. Each barrier has unintended weaknesses or holes. These weaknesses are random and constantly changing, and when, by chance, all holes are aligned, the failure reaches the final product or customers – resulting in accidents or near-misses.
In James Reason’s model, there are a few crucial conclusions:
- Human errors are inevitable because humans are inherently variable.
- Most of the errors are not the fault of a careless individual.
- Punishment culture is not an effective means of reducing human errors.
- All human error is a System Failure influenced by the work environment.
How do we create robust barriers?
Based on James Reason, organizations must have six layers of defense mechanisms:
- Good Documentations
- Clear Communications
- Robust Training Programs
- Accurate Operating Procedures
- Effective Supervision
- Effective Inspection or validation
Thus, to create a discipline quality and safety culture, organizations must first focus on systemizing how these six barriers are managed and governed.
For example, organizations need to simplify and streamline how their employees are:
- Retrieving documentation & SOP
- Trained on the shop floor, consistently and accurately to the SOP
- Supervised effectively throughout the training progression
- Certified or validated for their skills and competencies
System Fragmentation is a big “hole”
One of the biggest challenges we have seen with many organizations is the fragmentation of their training systems. Because of the complexity of shop floor training requirements, many organizations have patched several systems together to address their complex business needs. Often, this involves Excel sheets and manual data entries to capture and report on their workforce skills matrix. With fragmented systems, it is incredibly challenging to effectively create defense barriers in all six layers outlined by James Reason.
Implementing enterprise-wide Quality Training System
Consolidating fragmented, inconsistent training and certification practices into a centralized quality training system should be a high priority for manufacturers. The ideal system solution should have the following capabilities to create a foolproof quality system for your organization:
- Automate employee communication when changes are made to the SOP
- Seamlessly integrate with existing document control application
- Support all modalities of training delivery and content types
- Automatically manage reoccurring training frequencies and notification
- Creating a clear onboarding training curriculum tailored to different job roles
- Systemizing shop floor training, on-the-job training, and certification programs
- Providing supervisors with relevant reporting to make better workforce decisions
- Integrated testing, assessment, and survey functionalities
- Integrated skills audit and validation workflow with role management
- Robust database and reporting capability to meet the highest audit requirements
- A system capable of scaling up with the organization
By implementing a Quality Training System with these capabilities, you will create a stronger defense mechanism to ensure all failures and errors will be eliminated and/or caught before reaching the final customer.
With the right experienced solution partner, this investment should be a rapid and cost-effective exercise towards establishing a quality culture that supports your employees and meet the expectations of your customers in both quality and cost.
Seertech has pioneered an automated and structured technology solution called OJT3, designed to streamline and control the knowledge and skills transfer process. Leveraging the ‘Power of Three’- Plan, Execute, and Prove, OJT3 digitizes the entire OJT workflow, encompassing resource planning, bench capability analysis, and skills evidence capture.
If you like to explore more on how ourOJT3 framework can help you improve your overall quality and safety, please contact us today.
Recent articles
The Ultimate Guide to Tracking LMS Metrics
Understanding the Importance of LMS Metrics Understanding LMS metrics is crucial for the success and validation of your learning programs. LMS metrics offer key insights into the effectiveness of training initiatives, helping to provide concrete evidence of their value. With increasing pressure to demonstrate ROI, particularly from senior leadership and financial officers, tracking these [...]
Embracing the AI Shift in L&D
Introduction to AI in Learning and Development AI is revolutionizing Learning and Development (L&D) by transforming traditional learning methodologies into dynamic, performance-oriented strategies. Unlike conventional tools that merely expedite existing processes, AI offers a comprehensive overhaul of how learning initiatives are designed and implemented. The true potential of AI lies in its ability to [...]